Smart factory solutions and emerging digital technologies are poised to drive profound transformation across the manufacturing industry. Customers want personalized products and friction-free delivery – and this is driving manufacturers to leverage smart manufacturing, including AI and analytics, to rapidly assemble and deliver products. Industry 4.0 and 5.0 principles and the convergence of automation, cloud computing, AI and machine learning (ML), IIoT, AR and VR, cybersecurity and blockchain technology will enhance efficiency, security, scalability and connectivity in manufacturing operations.
Although the transition to smart factories may initially be slow and challenging, the long-term benefit of being able to respond quickly to changing customer demands makes smart manufacturing a compelling choice. Combining product, process and consumer data into one integrated, digital thread can deliver the kind of customized manufacturing at scale that has previously eluded the manufacturing sector.
The latest ISG Smart Manufacturing Survey finds the top reason enterprises undertake smart manufacturing is to improve productivity in their plant, processes and people. The second reason is cost savings and the third is supply chain resilience. Organizations of all sizes need greater visibility into data and operations so they can streamline processes and optimize labor effectiveness. To accomplish this, the manufacturers we spoke to say they plan to adopt agile development, IoT, predictive maintenance, machine learning and digital twin technologies over the next 24 months.
The chart below shows the findings when we asked organizations whether they had adopted, were piloting or evaluating a variety of smart manufacturing-related technologies.
Where Organizations Stand on the Smart Manufacturing Technology Adoption Journey
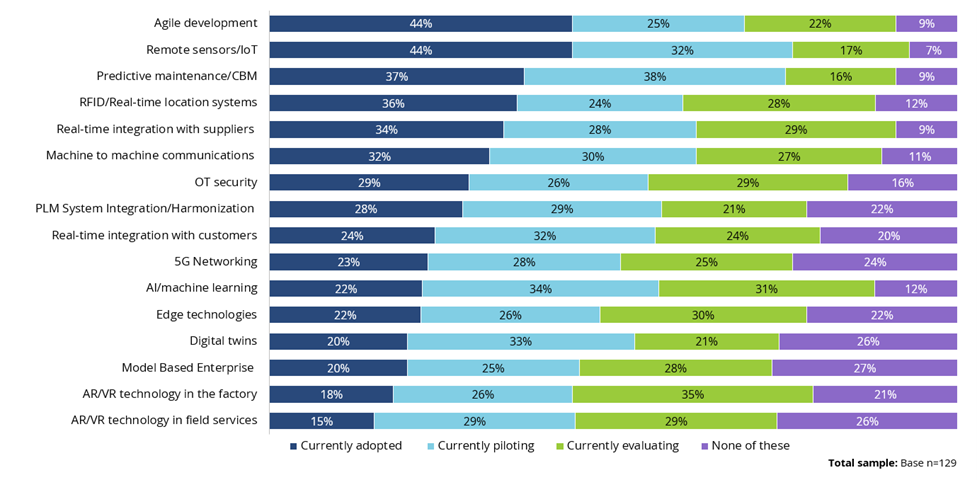
Source: 2023 ISG Smart Manufacturing Survey
Preparing Your Workforce
A skilled workforce is needed to manage these technologies. Before they can enjoy the business benefits of advanced technology, manufacturers must upskill and reskill factory workers to bridge the skill gap, enhance productivity and maintain global competitiveness. Virtual reality (VR) training is a cost-effective and efficient solution for teaching employees to use new equipment and procedures and significantly reduces the risks of production accidents and equipment failures. By allowing users to master multiple tools in realistic scenarios, VR simulations can cut training time and boost retention rates.
Traditional workers may also need training in data analysis and computer-aided technologies. Personalized training programs, tailored to individual learning styles and skill gaps, can foster workforce flexibility and resilience. Educational institutions, in collaboration with industry partners, play a critical role in providing real-world insights and practical applications of theoretical knowledge. For example: Georgia Tech has partnered with Boeing to work on advanced aerospace technologies. This collaboration provides students with opportunities to engage in cutting-edge research on topics like aerospace materials, propulsion systems and robotics. Carnegie Mellon University (CMU) partnered with General Motors (GM) on projects related to autonomous vehicles. This collaboration provides students with access to GM's automotive data, test vehicles and expertise. In corporate settings, both in-house training initiatives and collaboration with external training providers are vital for workforce development.
The Five Dimensions of Smart Manufacturing
Companies are continuing to expand their revenue through a shift to services, such as service contracts, maintenance contracts, extended warranties and even concierge services. As revenue models shift to service as a product, or technology-enabled products (IoT), the systems and data are increasingly center stage in our decision-making. They fundamentally transform decision-making by providing continuous, actionable insights from the data our smart products generate.
To truly benefit from smart manufacturing and change the way products are made, companies must address all five dimensions of smart manufacturing:
- Focus on the efficient development of digital products and services with an emphasis on digital aftermarket services. These may include services like remote product health management and providing tailored results to customers via software-enabled capabilities. For example: Tesla vehicles use software for over-the-air updates, remote diagnostics and autonomous driving, with sensor data continuously improving performance and safety.
- Invest in a fast-paced rollout and integration of products that are interconnected through advanced technologies, such as IoT, AI and cloud computing, are bringing about significant change across industries. Connected products are boosting efficiency, facilitating real-time data analysis and driving innovation across sectors such as healthcare, manufacturing, retail and transportation.
- Create smart digital factories that highlight efficiencies as compared to traditional brick and mortar structures.
- Institutionalize at scale digital backbones across the enterprise.
- Commit to an effective transition to a new operating model to maximize the benefits of technological advancements. The new model should be agile and adaptable to integrate innovations seamlessly.
Now that the capabilities are in place and the benefits are clear, manufacturers are increasing the number of smart manufacturing use cases, with most expecting their programs to be fully operational by 2025. More than 70% report they’ve achieved cost savings and improved the quality of manufacturing, and our survey results say benefits appear quickly—within 12 months in 81% of reported cases.
Smart manufacturing is both relatively new and already decidedly successful in transforming the way products are made. Technology is introducing efficiencies and cost savings into the manufacturing process, increasing speed to value in R&D initiatives and boosting top-line revenue growth with the rapid introduction of new products.
ISG helps manufacturing enterprises design a plan to navigate the rapidly changing tech landscape and put it to use for them. Contact us to start a conversation.